7 Benefits of Precast Parking Garage Construction

You may be familiar with the advantages of precast concrete, but how do they translate into benefits for a new parking garage? Whether you’re looking for a mixed-use space or a stand-alone structure, precast concrete can help you become more efficient, safe, and cost-effective.
Below, we’ll dive into the benefits of precast parking garage construction and current trends that align with these specific structures.
#1. Greater Interior Design Flexibility
One of the greatest benefits of a precast parking garage structure is the ability for fewer interior columns and ultimately, more space for more cars. We can accomplish this at High Concrete through longer bay areas and wider Double T spans.
Wider Double T’s ultimately reduce the cost of the foundation of your project. Because High Concrete offers a wider Double T surface area, there are fewer pieces needed for caulk joints and bays. This also gives your team flexibility in design so you can customize the space based on your client’s needs.
Trends in parking garage design point towards safety and higher visibility. With wider bay areas and fewer interior columns, there are fewer places for people to hide within the garage. And with 1 in every 10 property crimes happening in parking garages, this open area can be an additional boost to customer satisfaction.
On top of that, wider bays mean a flatter surface and better turn space. These are becoming increasingly popular because of the safety measures they provide. With flat surfaces, there’s less risk of users falling or not being able to see other cars and potentially turning the corner and getting into an accident.
Healthcare facilities, casinos, and malls are all noticing these benefits and choosing building materials that can provide larger bay areas and flat surfaces to increase driver safety.
#2. Extended Lifespan with Maintenance
The durability and resiliency of precast concrete exceed its counterparts. With proper maintenance and seasonal care, precast concrete parking garages can last between 50 and 60 years.
Engineers have suggested that the average lifespan of steel parking garages is around 30 years. When either type of parking garage goes without maintenance and exceeds its average lifespan, damages are expected to occur.
To ensure your structure lasts for decades, make sure to conduct annual inspections and reviews so you can be proactive about needed repairs. We also recommend washing your parking structure annually, especially to clean off snow and salt from the winter.
#3. Increased Construction Efficiency
In the construction industry, time is money. When projects are delayed or supplies are on backorder, your budget will suffer. Compared to steel and cast-in-place, precast parking structures can be built in half the time.
When using cast-in-place construction, the process of curing the concrete takes up to 28 days. In comparison, because precast concrete panels are made within a controlled facility and away from external elements, they can be cured within 48 hours.
Once we are on-site, a majority of the components of your precast parking garage are already built. On average, our team installs 12 to 15 panels a day. With our efficiency, a 400 - 500 car parking garage can be completely installed in under 3 months. From design, fabrication, and installation, High Concrete can complete an operational parking garage in 12 months.
Another benefit of construction efficiency is the reduced risk of injury on the work site. Because there are fewer trades needed on the work site and fewer moving parts, there’s less risk of common construction injuries or miscommunications.
#4. Getting the Full Picture From the Beginning
Unexpected costs and interruptions are fairly common in the construction industry. At High Concrete, we prioritize minimizing the risk of delays or extra costs by starting each project with a BIM design.
The preconstruction stage is essential for a smooth and hassle-free construction process. That is why we dedicate time to early design assistance so your team has a full understanding of what you’ll be buying and what precast concrete components will best benefit you.
This model also allows you to make adjustments before production starts. So minimal time and money are wasted when changes are needed. Our team works with a structural designer to plan our construction details such as loads, product samples, and value engineering.
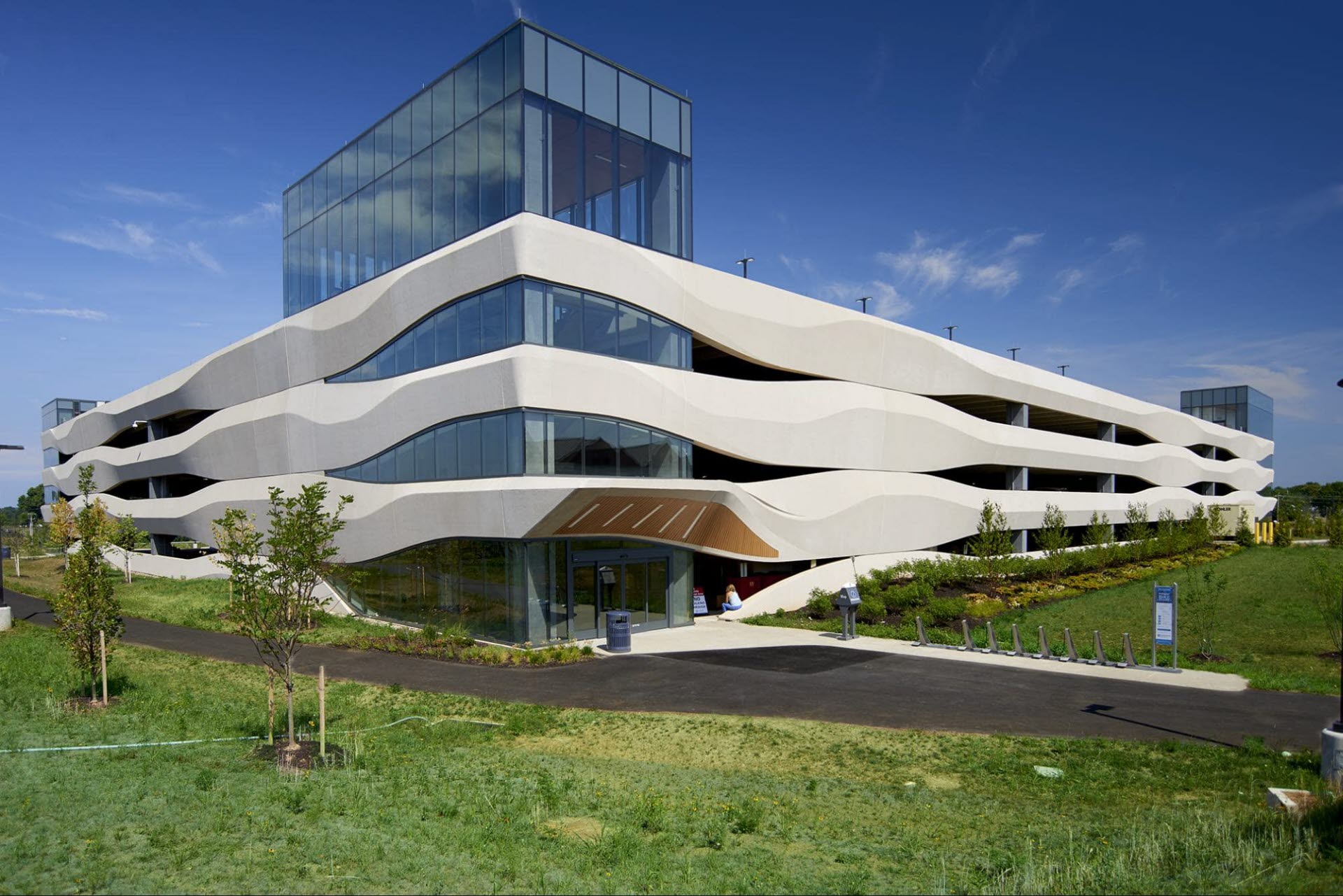
#5. Create the Look You Want
When you choose steel or cast-in-place for your building material, your design options are fairly limited. You’ll likely end up with a very industrial design for your garage structure that doesn’t have a lot of variability.
With precast concrete, you can redefine your parking garage design to either blend in with its surroundings or become a part of your company’s brand.
Whether you’re looking for brick, stone, or a specific color or finish, precast concrete can achieve it for you. High Concrete can even put emblems or text on your parking garage to integrate the structure with your company or community.
There are four different types of garage structures that High Concrete can construct to match your functional requirements and design requests.
- Stand Alone. This is the most common type of parking garage and acts as a stand-alone structure.
- Podium. A podium garage is best used in tight urban spaces where a parking garage supports a superstructure above. For example, this could be a hotel, mixed-use building, or office building.
- Mixed-Use. Have commercial space on the first floor and parking above, this provides additional revenue opportunity if your team decides to fill the commercial space.
- Residential Wrap. Your parking garage would be within other residential space, this type of garage is generally used to hide the structure and provide additional security.
Parking garages take up a significant percentage of city and urban space. To maintain the aesthetic appeal of your city, design a high-end structure that blends into the community or campus.
A popular structural type is mixed-use garages. This means there is commercial space on the first floor and parking above. The same benefits of a precast concrete parking garage apply to commercial buildings.
The mixed-use space provides flexibility for your city and precast concrete provides a larger building footprint.
#6. Keep Processes In-House
When multiple contractors are involved in a project, there’s an increased risk of miscommunications or delays. Also, there’s a higher chance of items getting backordered or not being completed on schedule.
Some of the most common construction issues come from material or labor shortages. These issues can be heightened if you’re working with multiple contractors and vendors.
Choosing High Concrete means building components are all completed through our facility or trusted partners. Garage structure components such as elevator boxes and stairs, can also be completed during High Concrete’s production.
Keeping some of these steps in-house creates construction efficiency and clear communication. You’ll know who your point of contact is and who to ask with questions and updates throughout the entirety of your project.
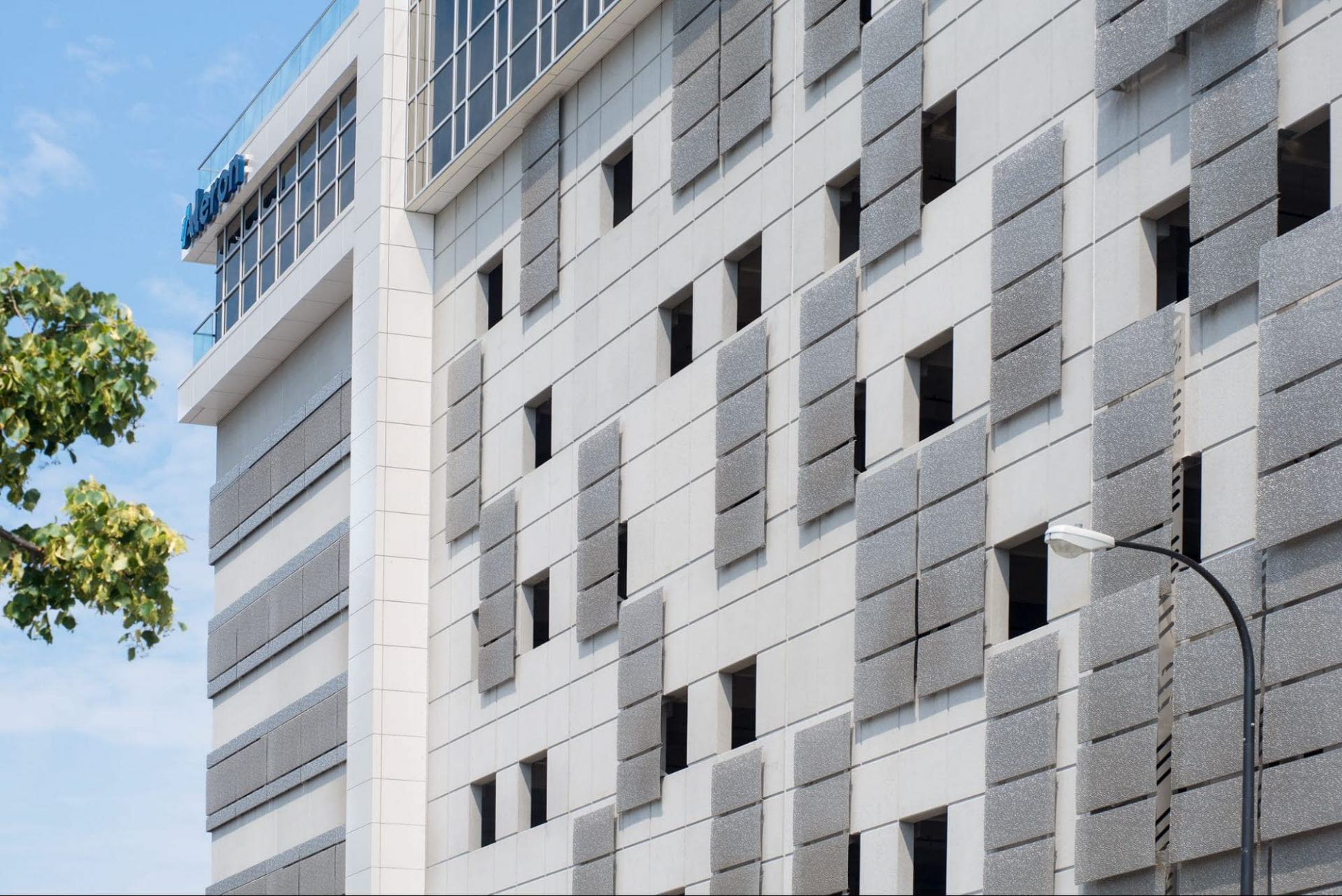
#7. Know You’re Getting High-Quality
Precast facilities, and High Concrete, are rated and scaled based on PCI standards. We’re proud to provide a superior product for a variety of categories.
Both High Concrete’s precast concrete facilities must be audited and toured to ensure we follow all the guidelines set in place by PCI. This guarantees to our clients that the work we do every day is high-quality and of a superior standard.
Not only are our facilities certified, but High Concrete only works with vendors of the same high standard. So, from start to finish, you can trust that we are supplying top-quality products to you.
Learn more about the benefits of precast parking garage construction and how High Concrete can help you.
